Двигатель наружного сгорания принцип работы: Двигатель Стирлинга — Википедия – Двигатель внешнего сгорания стирлинга: устройство, принципы работы и 3 модификации
Двигатель внешнего сгорания: виды, принцип работы, особенности
Двигатели внешнего сгорания стали использоваться тогда, когда людям потребовался мощный и экономичный источник энергии. До этого использовались паровые установки, однако они были взрывоопасными, так как использовали горячий пар под давлением. В начале 19 века им на смену пришли устройства с внешним сгоранием, а еще через несколько десятков лет были изобретены уже привычные приборы с внутренним сгоранием.
Происхождение устройств
В 19 веке человечество столкнулось с проблемой, которая заключалась в том, что паровые котлы слишком часто взрывались, а также имели серьезные конструктивные недостатки, что делало их использование нежелательным. Выход был найден в 1816 году шотландским священником Робертом Стирлингом. Эти устройства можно также называть «двигателями горячего воздуха», которые применялись еще в 17 веке, однако этот человек добавил к изобретению очиститель, называющийся в настоящее время регенератором. Таким образом, двигатель внешнего сгорания Стирлинга был способен сильно повысить производительность установки, так как он сохранял тепло в теплой рабочей зоне, в то время как рабочее тело охлаждалось. Из-за этого эффективность работы всей системы была значительно увеличена.
В то время изобретение использовалось достаточно широко и находилось на подъеме своей популярности, однако со временем его перестали использовать, и о нем забыли. На смену оборудованию внешнего сгорания пришли паровые установки и двигатели, но уже привычные, с внутренним сгоранием. Вновь о них вспомнили лишь в 20 веке.

Работа установки
Принцип работы двигателя внешнего сгорания заключается в том, что в нем постоянно чередуются два этапа: нагревание и охлаждение рабочего тела в замкнутом пространстве и получение энергии. Данная энергия возникает из-за того, что постоянно изменяется объем рабочего тела.
Чаще всего рабочим веществом в таких устройствах становится воздух, однако возможно использование еще и гелия или водорода. В то время пока изобретение находилось на стадии разработки, в качестве опытов использовались такие вещества, как двуокись азота, фреоны, сжиженный пропан-бутан. В некоторых образцах пытались применять даже обычную воду. Стоит отметить, что двигатель внешнего сгорания, который запускали с водой в качестве рабочего вещества, отличался тем, что у него была достаточно высокая удельная мощность, высокое давление, а сам он был достаточно компактным.

Первый тип двигателя. «Альфа»
Первой моделью, которая использовалась, стала «Альфа» Стирлинга. Особенность его конструкции состоит в том, что она имеет два силовых поршня, находящихся в разных в раздельных цилиндрах. Один из них имел достаточно высокую температуру и был горячим, другой, наоборот, холодным. Внутри теплообменника с высокой температурой располагалась горячая пара цилиндр-поршень. Холодная пара находилась внутри теплообменника с низкой температурой.
Основными преимуществами теплового двигателя внешнего сгорания стало то, что они имели высокую мощность и объем. Однако температура горячей пары при этом была слишком велика. Из-за этого возникали некоторые технические трудности в процессе изготовления таких изобретений. Регенератор данного устройства находится между горячей и холодной соединительными трубками.

Второй образец. «Бета»
Вторым образцом стала модель «Бета» Стирлинга. Основное конструктивное отличие заключалось в том, что имелся лишь один цилиндр. Один из его концов выполнял роль горячей пары, а другой конец оставался холодным. Внутри данного цилиндра перемещался поршень, с которого можно снимать мощность. Также внутри имелся вытеснитель, который отвечал за изменение объема горячей рабочей зоны. В данном оборудовании использовался газ, который перекачивался из холодной зоны в горячую через регенератор. Этот вид двигателя внешнего сгорания обладал регенератором в виде внешнего теплообменника или же совмещался с поршнем-вытеснителем.

Последняя модель. «Гамма»
Последней разновидностью данного двигателя стала «Гамма» Стирлинга. Этот тип отличался не только наличием поршня, а также вытеснителя, а еще и тем, что в его конструкцию входили уже два цилиндра. Как и в первом случае один из них был холодным и использовался он для отбора мощности. А вот второй цилиндр, как в предыдущем случае, был холодным с одного конца и горячим с другого. Здесь же перемещался вытеснитель. В поршневом двигателе внешнего сгорания также имелся регенератор, который мог быть двух типов. В первом случае он был внешним и соединял между собой такие конструктивные части, как горячую зону цилиндра с холодной, а также с первым цилиндром. Второй тип – это внутренний регенератор. Если использовался этот вариант, то он входил в конструкцию вытеснителя.
Использование Стирлингов обосновано в том случае, если необходим простой и небольшой преобразователь тепловой энергии. Также его можно использовать в том случае, если разница температур недостаточно велика, чтобы использовать газовые или же паровые турбины. Стоит отметить, что на сегодняшний день такие образцы стали использоваться чаще. К примеру, используются автономные модели для туристов, которые способны работать от газовой конфорки.

Применение устройств в настоящее время
Казалось бы, что такое старое изобретение не может использоваться в наши дни, однако это не так. NASA заказало двигатель внешнего сгорания типа Стирлинга, однако в качестве рабочего вещества должны использоваться ядерные и радиоизотопные источники тепла. Кроме этого, он также успешно может быть использован в следующих целях:
- Использовать такую модель двигателя для перекачки жидкости гораздо проще, чем обычный насос. Во многом это благодаря тому, что в качестве поршня можно применять саму перекачиваемую жидкость. Кроме того, она же и будет охлаждать рабочее тело. К примеру, такой вид «насоса» можно использовать, чтобы накачивать воду в ирригационные каналы, используя для этого солнечное тепло.
- Некоторые изготовители холодильников склоняются к установке таких устройств. Стоимость продукции удастся снизить, а в качестве хладагента можно применять обычный воздух.
- Если совместить двигатель внешнего сгорания этого типа с тепловым насосом, то можно оптимизировать работу тепловой сети в доме.
- Довольно успешно Стирлинги используются на подводных лодках ВМС Швеции. Дело в том, что двигатель работает на жидком кислороде, который впоследствии используется для дыхания. Для подводной лодки это очень важно. К тому же такое оборудование обладает достаточно низким уровнем шума. Конечно, агрегат достаточно большой и требует охлаждения, но именно эти два фактора несущественны, если речь идет о подводной лодке.

Преимущества использования двигателя
Если во время конструирования и сборки применить современные методы, то удастся поднять коэффициент полезного действия двигателя внешнего сгорания до 70%. Использование таких образцов сопровождается следующими положительными качествами:
- Удивительно, однако крутящий момент в таком изобретении практически не зависит от скорости вращения коленчатого вала.
- В данном силовом агрегате отсутствуют такие элементы, как система зажигания и клапанная система. Также здесь отсутствует распредвал.
- Достаточно удобно то, что на протяжении всего периода использования не потребуется проводить регулировку и настройку оборудования.
- Данные модели двигателя не способны «заглохнуть». Простейшая конструкция аппарата позволяет использовать его достаточно продолжительное время в полностью автономном режиме.
- В качестве источника энергии можно использовать практически все, начиная от дров и заканчивая урановым топливом.
- Естественно, что в двигателе внешнего сгорания процесс сжигания веществ осуществляется снаружи. Это способствует тому, что топливо дожигается в полном объеме, а количество токсических выбросов минимизируется.

Недостатки
Естественно, что любое изобретение не лишено недостатков. Если говорить о минусах таких двигателей, то они заключаются в следующем:
- Из-за того что сгорание осуществляется вне двигателя, отвод получаемого тепла происходит через стенки радиатора. Это вынуждает увеличивать габариты устройства.
- Материалоемкость. Для того чтобы создать компактную и эффективную модель двигателя Стирлинг, необходимо иметь качественную жаропрочную сталь, которая сможет выдержать большое давление и высокую температуру. Кроме того, должна быть низкая теплопроводность.
- В качестве смазки придется покупать специальное средство, так как обычное коксуется при высоких температурах, которые достигаются в двигателе.
- Для получения достаточно высокой удельной мощности придется использовать либо водород, либо гелий в качестве рабочего вещества.
Водород и гелий в качестве топлива
Получение высокой мощности, конечно же, необходимо, однако нужно понимать, что использование водорода или гелия достаточно опасно. Водород, к примеру, сам по себе достаточно взрывоопасен, а при высоких температурах он создает соединения, которые называются металлогидритами. Это происходит, когда водород растворяется в металле. Другими словами, он способен разрушить цилиндр изнутри.
Кроме того, и водород, и гелий – это летучие вещества, которые характеризуются высокой проникающей способностью. Если говорить проще, то они достаточно легко просачиваются сквозь практически любые уплотнения. А потери вещества означают потери в рабочем давлении.
Роторный двигатель внешнего сгорания
Сердце такой машины – это роторная машина расширения. Для двигателей с внешним типом сгорания этот элемент представлен в виде полого цилиндра, который с обеих сторон прикрыт крышками. Сам по себе ротор имеет вид колеса, который посажен на вал. Также у него имеется определенное количество П-образных выдвигающихся пластин. Для их выдвижения используется специальное выдвижное устройство.
Двигатель внешнего сгорания Лукьянова
Юрий Лукьянов – это научный сотрудник Псковского политехнического института. Он уже достаточно давно занимается разработкой новых моделей двигателей. Ученый старался сделать так, чтобы в новых моделях отсутствовали такие элементы, как коробка передач, распредвал и выхлопная труба. Основной недостаток устройств Стирлинга заключался в том, что они имели слишком большие габариты. Именно этот недостаток ученому и удалось устранить за счет того, что лопасти были заменены на поршни. Это помогло уменьшить размер всей конструкции в несколько раз. Некоторые говорят о том, что можно сделать двигатель внешнего сгорания своими руками.
Роторные двигатели внешнего сгорания
Первые тепловые машины созданные человечеством были машинами внешнего сгорания. Они широко (для того времени) использовались в различных отраслях промышленности и на транспорте. Как правило, основой преобразования энергии газа во вращательное движение была кинематика поршневого двигателя с кривошипно-шатунным механизмом. После создания двигателей внутреннего сгорания, сфера применения двигателей с внешним подводом тепла значительно сократилась. В последнее время в связи с развитием технологии, появлением новых материалов появились перспективы реализовать потенциальные возможности двигателей внешнего сгорания. Их относительная экологическая чистота, возможность применения помимо традиционного другого разнообразного топлива или источников тепла (солнечной, ядерной энергии) меньшая шумность возродила интерес к ним.
Одним из самых конструктивно и технологически проработанным (не считая турбин) двигателем внешнего сгорания является двигатель Стирлинга, который к тому же имеет довольно высокий теоретический (до 70 %) КПД. Правда, основные модификации (альфа, бета, гамма) таких двигателей конструктивно сложны и громоздки, а схема преобразования теплоты, содержащейся в топливе, предполагает значительные потери механической энергии, и небольшую по сравнению с обычным ДВС, удельную мощность. Кроме того, сложно решить вопросы уплотнения и герметизации рабочего тела. И попытки обойти эти проблемы в существующих схемах, даже с учетом новых технологий, пока не привели к созданию конкурентоспособной с обычным ДВС силовой установки.
Авторы предлагают варианты схем построения двигателей внешнего сгорания, лишенных, на их взгляд, некоторых из вышеописанных, существенных недостатков. Такие схемы позволяют иметь высокие удельные характеристики двигателей, меньшие требования к уплотнениям, использование распространенных компонент в качестве рабочего тела и более низкие значения средних давлений цикла без потери эффективности
Первое – однонаправленностьпроцесса исключает потери, связанные с изменением направления движения рабочего тела. Возвратно–поступательное движение поршневой машины (большинство построенных двигателей имеет этот тип кинематики), создает и соответственное движение рабочего тела. А это, при больших паразитных объемах и на высоких частотах вращения, приводит к уменьшению перемещаемой массы рабочего тела в системе согласно тактам цикла. В существующих двигателях с возвратно поступательным движением, порции рабочего тела не могут в цикле находится более чем в двух смежных тактах. Приходится резко ограничивать объемы теплообменников и трубопроводов. Ограничение объемов теплообменников свою очередь ведет к снижению скорости теплообмена. И тогда, для построения двигателей с высокими удельными характеристиками полученных за счет значительных оборотов, надо использовать рабочее тело с большим коэффициентом теплопередачи (водород, гелий). А ограничение объемов трубопроводов приводит к большим газодинамическим потерям (уменьшение проходного сечения).
Однонаправленность, же позволяет иметь в устоявшемся режиме относительно постоянную скорость рабочего тела в системе и темне позволяет пружинить рабочим телом, что значительно уменьшает потери от паразитных объемов. Используя это свойство можно иметь в теплообменнике 2-3 «порций» рабочего тела. Отсюда, при сквозном проходе рабочего тела по закольцованному контуру, время теплообмена можно увеличить в 2-3 раза, и при этом иметь более развитую площадь теплообмена за счет больших теплообменников. А это в свою очередь увеличит и скорость теплообмена. Похожие схемы имеют двигатель Нисковских и частично Цвауэра.
Второе – параллелизм,
В итоге, реализуя оба свойства длительность теплообмена можно увеличить на порядок. А это – повышение удельных показателей двигателей использующих доступный газ, к примеру азот (воздух) на уровень двигателей, где в качестве рабочего тела используется вещество с большим коэффициентом передачи теплоты (водород и гелий). И поэтому появляется возможность создания относительно дешевых двигателей с высокими удельными характеристиками, с меньшими требованиями к уплотнениям, с функцией компенсации потери рабочего тела(воздух) и поддержании среднего давления цикла посредством подкачки (компрессор с независимым приводом или от двигателя, ресивер и т.д.) из атмосферы. Кроме того, более высокая масса воздуха (по сравнению с водородом), при однонаправленном движения рабочего тела, способствует накоплении энергии, чем выравниваются возникающие пульсации потока.
Естественно в качестве рабочего тела можно использовать и другие газы, а с применением водорода или гелия можно кратно увеличить удельную мощность (за счет оборотов) по отношению к существующим двигателям, до пределов механических ограничений.
Сердце данных двигателей его силовая часть, основа преобразования – роторная машина расширения (Рис.1).
Машина расширения для двигателя внешнего сгорания содержит неподвижный корпус представляющий полый цилиндр, который с торцов прикрыт крышками, ротор в виде посаженного на вал колеса и имеющего
Конструктивные особенности машины расширения позволяют иметь довольно значительные объемы полостей, при небольших общих габаритах. Самым оптимальным является трехлопаточный вариант, (и при дальнейшем увеличении лопаток — кратно трем) обеспечивающий при минимальном диаметре ротора максимальное значение опорной части лопаток при их полном выдвижении, и наибольшую величину этого выдвижения.
Механизм ВУ обладает несложной кинематикой и суть вспомогательное устройство, а не элемент преобразования энергии, и служит для согласования выдвижения лопаток с углом поворота ротора. Механизм ВУ не подвергается большим динамическим нагрузкам и не является источником значительных механических потерь.
Герметизацию полостей машины расширения можно обеспечить путем лабиринтных уплотнений. В внутриободном пространстве ротора можно иметь избыточное давление без потерь КПД ( в отличии альфа модификаций, где подпоршневое давление в картере уменьшает КПД). Лопатки находятся в закрытых (изолированных от внутриободного пространства ротора) каналах расположенных в спицах с выходом только в рабочие полости и соединенных с элементами ВУ (толкателями) через легко уплотняемые штоки. Последние, в свою очередь, могут быть защищены гофрированными втулками от масла. Внутриободное пространство ротора в свою очередь должно быть отделено (не показано) от подверженного смазке около осевого пространства (где расположены элементы ВУ). В каналах лопаток (лучше с выталкивающей стороны) расположены желобки, для подвода рабочего тела к тыльной грани лопаток, что бы избежать тормозящего разряжения.
Работа машины расширения осуществляется следующим образом (Рис.2).
Рабочее тело через впускное окно подается в рабочую полость и, воздействуя на заднюю грань (по ходу вращения) лопатки, заставляет ротор вращаться. А в дальнейшем лопатка своей передней гранью выталкивает отработанное рабочее тело через выпускное окно, чем обеспечивается его прямоточное движение внутри расширительной машины.
Построение двигателя как комбинации нескольких размещенных на одном валу модулей (секций машин расширения) с подобранными объемами полостей и расположением зон нагрева и охлаждения, позволяет задать любой термодинамический цикл его работы (с учетом параметров рабочего тела, конструкционных материалов, и используемого топлива), к примеру цикл Стирлинга, Эриксона и т.д. Варианты схем построения двигателей ограниченны только рациональностью и здравым смыслом и показывают гибкость данной конструкции.
Классический цикл Стирлинга реализуется в двигателе, в котором на всех этапах цикла используется только газообразное рабочее тело с четырьмя переменными объемами и с использованием регенераторов (Рис3. схема построения).
Двигатель составлен из последовательно расположенных на одном валу секций-модулей Si (где i = 1,2…k), каждая из которых имеет N полостей определенного (условного) объема Vi. И двигатель состоит из двух четко разделенных частей. Одна – нагревается (горячая) Dh, а другая – охлаждается (холодная) Dc..
Для предотвращения потерь связанных с холостым проходом рабочего тела рабочих полостей, в модуле расширения (или в других модулях в зависимости от цикла), при нахождении лопаток в зоны перехода, нужна перекрывающая задвижка перед впускным окном соответствующего модуля. Диск регенератора также может исполнять роль запирающей задвижки, перекрывающей трубопровод в момент прохождения лопаткой зону перехода, когда соответствующий сектор будет глухо закрыт пластиной.
Нагрев рабочего тела происходит в нагревателе Hот любого источника тепла ((в представленном – горелки). Охлаждение рабочего тела в холодильнике С посредством охлаждающей жидкости с последующим отводом тепла через радиатор Rd. Нагрев и охлаждение также захватывают стенки модулей в соответствии расположении последних в определенных зонах (частях ) двигателя. Для более эффективного использования тепла рабочего тела служит и предварительный теплообменник НС 1 выравнивающий температуру отходящего и входящего потока рабочего тела. Для регулировки мощности служит золотник Z , управляемый посредством штока, и перепускной канал, соединяющий выпускной трубопровод секции S1 с впускным. Выдвигаясь, при регулировании, золотник отсекает часть потока рабочего тела выходящего из модуля «холодного» отдела и следующего в «теплый» и возвращает во входящий трубопровод данного модуля. Тем самым определяется количество рабочего тела проходящего через зону нагрева, что и соответственно влияет на изменение мощности с высокой степенью реакции.
Подвод воздуха к горелкам (для источников тепла требующих кислород) происходит посредством нагнетателя, через воздушный регенератор Rg 2( построенного аналогично Rg 1) и встроенного в противонаправленные каналы подвода воздуха и отвода отработанных газов. Тем самым идет подогрев воздуха к горелкам и уменьшаются тепловые потери. Для той же цели также используется и воздушный предварительный теплообменник НС 2. Такая обвязка позволяет максимально исключить (уменьшить) тепловые потери.
В данном исполнении термодинамический цикл, благодаря синфазности выдвижения лопаток будет более полно соответствовать теоретическому циклу Стирлинга.
Полезная работа двигателя будет
L= Pср. h (V2 –V1) – Pср.c(V3 – V4) – Lспр.
где, Pср. h — среднее давление в горячем отделе
Pср.c — среднее давление в холодном отделе
Pср. h = Pср.c *(T2 ) / (T1 ) ,
где T1 — температура (K) холодильника ( в отделе C), T2 – температура (K) нагревателя (в отделе H)
L спр. – работа сил механического, газодинамического и др. сопротивления.
Мы уже отмечали гибкость системы для построения двигателей по различным термодинамическим циклам. И, как вариант, исключим одну малую «горячую» секцию с условным объемом V2.Образующая система с подобранными объемами V1, V3. V4. и рабочим процессом при трех тактах будет реализовывать следующий термодинамический (в теории естественно) цикл.
Это естественно, приведет к некоторой потере эффективности. Но, помимо упрощения конструкции двигателя и снижения его массогабаритных показателей, можно иметь важное преимущество. В «горячей» области в секции с условным объемом V3, давление, перед и после лопатки существенно не различимо (естественно будут определенные незначительные отклонения). Отсюда в самой термически нагруженной части двигателя значительно упрощаются требования к уплотнениям лопаток. Достаточно иметь технологические зазоры (как в турбине) между стенками рабочей полости и торцами лопатки. Это возможно, так как выдвижение лопаток согласованно с углом поворота ротора. А в оставшихся «холодной» секции с почти «комнатной» температурой, проблемы уплотнений (включая материал изготовления) решить значительно проще.
Также можно позволяют построить паровой двигатель с использованием регенераторов (общий вид рис.1).
В двигателе, в качестве рабочего тела используются две компоненты, одна постоянно пребывающая в цикле в газообразном состоянии — газовый носитель, и компоненты изменяющей свое фазовое состояние. Газовая составляющая в двухобъемном варианте, может и не является рабочим телом. Это несущая и вспомогательная субстанция позволяющая использовать регенераторы в паровой машине. И газовая составляющая изначально находится при повышенном давлении.
Для построения данного двигателя используем две секции (модуля), первая S1 с условным объемом V1 является насосом газовой составляющей, а вторая S3 с условным большим объемом V3- непосредственно машина расширения (Рис.5).
Рабочее тело (в газообразном состоянии) с газовым носителем, пройдя после расширения регенератор Rg 1, в конденсаторе-сепараторе Cs, конденсируется и становится жидкостью, а газовая составляющая попадает в малую «холодную» секцию S1 (V1).
На выходе этой секции перед регенератором или через открытый торец его обода компоненты опять смешиваются, там жидкообразная распыляется форсункой F, а газовая несущая позволяет создавать направленность потока и осуществляет перенос компоненты изменяющей фазовое состояние.
Трубопровод перед регенератором разделен камеры таким образом сначала в первой камере (по чередованию прохождения насадки) происходит смешивание компонент. Пройдя регенератор жидкая составляющая опять становится газом (паром), и поступает через нагреватель в зону расширения всекцию S3 (V3). В итоге получается паровая машина с регенераторами, где газовая составляющая является постоянной компонентой замкнутого цикла. Форсунка Fa расположенная в зоне нагрева служит для максимально быстрого изменения – акселерации (увеличения) мощности.
Если задействовать в паровой машине три секции(и более) получим более перспективное направление – двигатели, использующие смешанное двухкомпонентное рабочее тело. Здесь газовая компонента суть рабочее тело, иуже будет совершать работу, содействуя приросту КПД. Наиболее перспективным выглядит двухкомпонентный двигатель и с тремя секциями S1,S3,S4 с условными объемами V1, V3 , V4 (Рис.6).
Основным достоинством такого рабочего тела является возможность получения при существующих уровнях среднего давления рабочего тела удельной мощности, почти в 2 раза большей, чем в случае однокомпонентного газового топлива. Кроме того, процессы парообразования и конденсации, наблюдаемые при фазовом переходе компонентов, характеризуется высокими коэффициентами теплоотдачи. Поэтому процессы сжатия и расширения в большей степени приближенны к изотермическим, чем в цикле с газовым рабочим телом. Важно и то, что при этом значительно (на две-три сотни градусов) снижается максимальная температура цикла и начальное давление газообразного рабочего тела. При этом чувствительность мощности двигателя к изменению «мертвого» объема оказывается чрезвычайно низкой.
Таким образомширокий выбор вариантов построения двигателя с определенным циклом, способом организации рабочего процесса, при однонаправленном движением рабочего тела, в сочетании с простотой расширительной машины и использованием вращающихся регенераторов позволяет с помощью дешевых и доступных материалов добиться повышения КПД и удельных характеристик двигателя. Сохраняя при этом уже известные достоинства двигателей данного типа– малошумность, «всеядность», высокий крутящий момент в очень широком диапазоне частот вращения выходного вала, увеличенный ресурс и низкие затраты на обслуживание при длительной эксплуатации. А указанные способы регулирования мощности позволяют применять данный двигатель не только в качестве стационарной силовой установки, но и стать реальной альтернативой мобильным (транспортным) ДВС.
Литература.
- Уокер Г. Пер.с англ. – М.: Машиностроение,1985.
- Г.Т.Ридер, Ч.Хупер.. М., Наука, 1986.
- Двигатели Стирлинга / [В.Н. Даниличев, С.И. Ефимов, В.А. Звонок и др.]; под ред. М.Г. Круглова. – М.: «Машиностроение», 1977.
- Патент РФ 2454546. Роторный преобразователь энергии и двигатель внешнего сгорания с его использованием. Чантурия И.Г., Чантурия О.Г.
О.ЧАНТУРИЯ, И.ЧАНТУРИЯ.
Двигатель Стирлинга – принцип работы. Низкотемпературный двигатель Стирлинга (фото)
Двигатель Стирлинга, принцип работы которого качественно отличается от привычного для всех ДВС, когда-то составлял последнему достойную конкуренцию. Однако на какое-то время о нем забыли. Как этот мотор используется сегодня, в чем заключается принцип его действия (в статье можно найти также чертежи двигателя Стирлинга, наглядно демонстрирующие его работу), и каковы перспективы применения в будущем, читайте ниже.
История
В 1816 году в Шотландии Робертом Стирлингом была запатентована тепловая машина, названная сегодня в честь своего изобретателя. Первые двигатели горячего воздуха были изобретены еще до него. Но Стирлинг добавил в устройство очиститель, который в технической литературе называется регенератором, или теплообменником. Благодаря ему производительность мотора возрастала при удерживании агрегата в тепле.
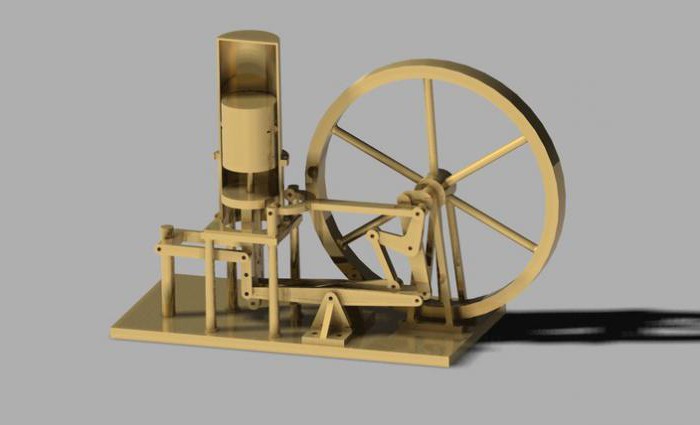
Двигатель признали наиболее прочной паровой машиной из имеющихся на тот момент, так как он никогда не взрывался. До него на других моторах такая проблема возникала часто. Несмотря на быстрый успех, в начале двадцатого столетия от его развития отказались, так как он стал менее экономичным, по сравнению с появившимися тогда другими двигателями внутреннего сгорания и электродвигателями. Однако Стирлинг еще продолжал применяться в некоторых производствах.
Двигатель внешнего сгорания
Принцип работы всех тепловых моторов заключается в том, что для получения газа в расширенном состоянии необходимы большие механические усилия, чем при сжатии холодного. Для наглядной демонстрации этого можно провести опыт с двумя кастрюлями, наполненными холодной и горячей водой, а также бутылкой. Последнюю опускают в холодную воду, затыкают пробкой, затем переносят в горячую. При этом газ в бутылке начнет выполнять механическую работу и вытолкнет пробку. Первый двигатель внешнего сгорания основывался на этом процессе полностью. Правда, позже изобретатель понял, что часть тепла можно применять для подогрева. Таким образом, производительность значительно возросла. Но даже это не помогло двигателю стать распространенным.
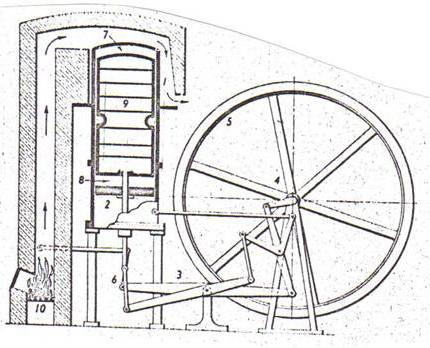
Позже Эриксон, инженер из Швеции, усовершенствовал конструкцию, предложив охлаждать и нагревать газ при постоянном давлении вместо объема. В результате немало экземпляров стало использоваться для работы в шахтах, на судах и в типографиях. Но для экипажей они оказались слишком тяжелыми.
Двигатели внешнего сгорания от Philips
Подобные моторы бывают следующих типов:
- паровой;
- паротурбинный;
- Стирлинга.
Последний вид не стали развивать из-за небольшой надежности и остальных не самых высоких показателей по сравнению с появившимися другими типами агрегатов. Однако в 1938 году компания Philips возобновила работу. Двигатели стали служить для приводов генераторов в неэлектрофицированных районах. В 1945 году инженеры компании нашли им обратное применение: если вал раскручивать электромотором, то охлаждение головки цилиндров доходит до минус ста девяносто градусов по Цельсию. Тогда решено было применять в холодильных установках усовершенствованный двигатель Стирлинга.
Принцип работы
Действие мотора заключается в работе по термодинамическим циклам, в которых при разной температуре происходит сжатие и расширение. При этом регулирование потоком рабочего тела реализуется за счет изменяющегося объема (или давления – в зависимости от модели). Таков принцип работы большинства подобных машин, которые могут иметь разные функции и конструктивные схемы. Двигатели могут быть поршневыми или роторными. Машины с их установками работают в качестве тепловых насосов, холодильников, генераторов давления и так далее.
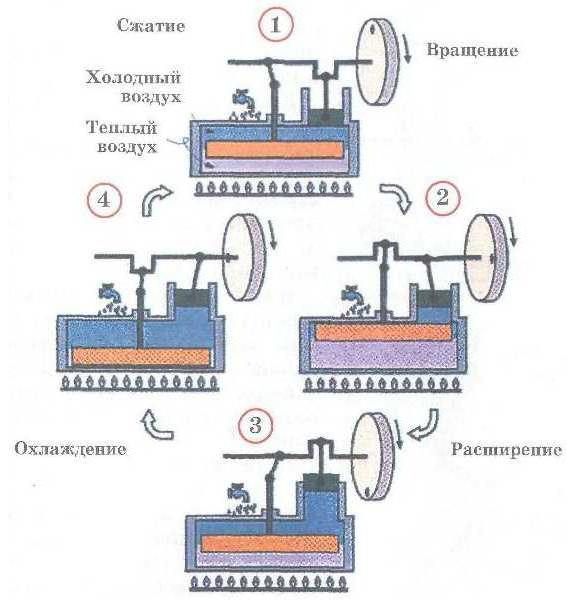
Помимо этого, есть моторы с открытым циклом, где регулирование потоком реализуется посредством клапанов. Именно их называют двигателями Эриксона, кроме общего названия имени Стирлинга. В ДВС полезная работа осуществляется после предварительного сжатия воздуха, впрыска топлива, нагрева полученной смеси вперемешку со сгоранием и расширения.
Двигатель Стирлинга принцип работы имеет такой же: при низкой температуре происходит сжатие, а при высокой – расширение. Но по-разному осуществляется нагрев: тепло подводится через стенку цилиндра извне. Поэтому он и получил название двигателя внешнего сгорания. Стирлинг применял периодическое изменение температуры с вытеснительным поршнем. Последний перемещает газ с одной полости цилиндра в другую. С одной стороны, температура постоянно низкая, а с другой – высокая. При передвижении поршня вверх газ перемещается из горячей в холодную полость, а вниз – возвращается в горячую. Сначала газ отдает много тепла холодильнику, а затем от нагревателя получает столько же, сколько отдал. Между нагревателем и холодильником размещается регенератор – полость, наполненная материалом, которому газ отдает тепло. При обратном течении регенератор возвращает его.

Система вытеснителя соединена с рабочим поршнем, сжимающим газ в холоде и позволяющим расширяться в тепле. За счет сжатия в более низкой температуре происходит полезная работа. Вся система проходит четыре цикла при прерывистых движениях. Кривошипно-шатунный механизм при этом обеспечивает непрерывность. Поэтому резких границ между стадиями цикла не наблюдается, а КПД двигателя Стирлинга не уменьшается.
Учитывая все вышесказанное, напрашивается вывод, что этот двигатель является поршневой машиной с внешним подводом тепла, где рабочее тело не покидает замкнутое пространство и не заменяется. Чертежи двигателя Стирлинга хорошо иллюстрируют устройство и принцип его действия.
Детали работы
Солнце, электричество, ядерная энергия или любой другой источник тепла может подводить энергию в двигатель Стирлинга. Принцип работы его тела заключается в применении гелия, водорода или воздуха. Идеальный цикл обладает термическим максимально возможным КПД, равным от тридцати до сорока процентов. Но с эффективным регенератором он сможет работать и с более высоким КПД. Регенерацию, нагрев и охлаждение обеспечивают встроенные теплообменники, работающие без масел. Следует отметить, что смазки двигателю нужно очень мало. Среднее давление в цилиндре составляет обычно от 10 до 20 МПа. Поэтому здесь требуется отличная уплотнительная система и возможность попадания масла в рабочие полости.
Сравнительная характеристика
В большинстве работающих сегодня двигателей подобного рода используется жидкое топливо. При этом непрерывное давление легко контролировать, что способствует снижению уровня выбросов. Отсутствие клапанов обеспечивает бесшумную работу. Мощность с массой сопоставимы моторам с турбонаддувом, а удельная мощность, получаемая на выходе, равна показателю дизельного агрегата. Скорость и крутящий момент не зависят друг от друга.
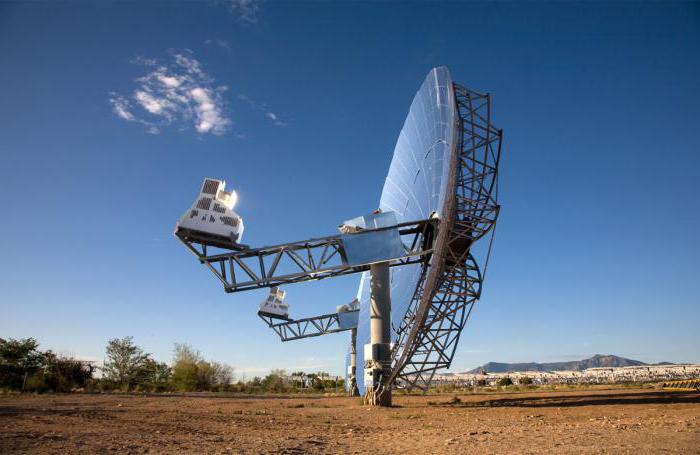
Затраты на производство двигателя гораздо выше, чем на ДВС. Но при эксплуатации получается обратный показатель.
Преимущества
Любая модель двигателя Стирлинга имеет много плюсов:
- КПД при современном проектировании может доходить до семидесяти процентов.
- В двигателе нет системы высоковольтного зажигания, распределительного вала и клапанов. Его не нужно будет регулировать в течение всего срока эксплуатации.
- В Стирлингах нет того взрыва, как в ДВС, который сильно нагружает коленвал, подшипники и шатуны.
- В них не бывает того эффекта, когда говорят, что «двигатель заглох».
- Благодаря простоте прибора его можно эксплуатировать в течение длительного времени.
- Он может работать как на дровах, так и с ядерным и любым другим видом топлива.
- Сгорание происходит вне мотора.
Недостатки
- Главным минусом конструкции является ее материалоемкость.
- Рабочее тело нужно охлаждать, из-за чего габариты существенно увеличиваются.
- Для получения равных с ДВС характеристик необходимо использовать высокое давление.
- К рабочему телу тепло подводят через стенки теплообменников, у которых ограниченная теплопроводность.
- Чтобы изменить мощность двигателя, изменяют объем буферной емкости, среднее давление рабочего тела, фазного угла между вытеснителем и поршнем.
Применение
В настоящее время двигатель Стирлинга с генератором используют во многих областях. Это универсальный источник электрической энергии в холодильниках, насосах, на подводных лодках и солнечных электрических станциях. Именно благодаря применению различного вида топлива имеется возможность его широкого использования.
Возрождение
Эти двигатели снова стали развиваться благодаря компании Philips. В середине двадцатого века с ней заключила договор General Motors. Она вела разработки для применения Стирлингов в космических и подводных устройствах, на судах и автомобилях. Вслед за ними другая компания из Швеции, United Stirling, стала заниматься их развитием, включая и возможное использование на легковых автомобилях.
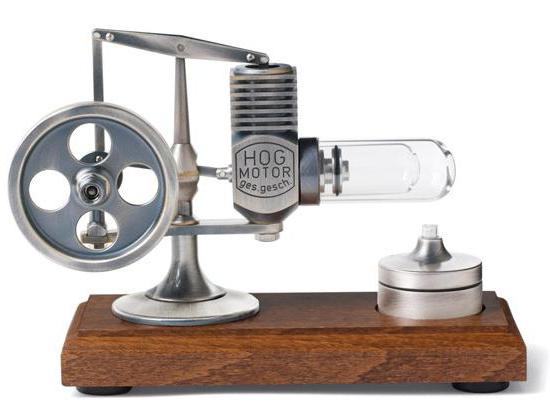
Сегодня линейный двигатель Стирлинга применяется на установках подводных, космических и солнечных аппаратов. Большой интерес к нему вызван из-за актуальности вопросов ухудшения экологической обстановки, а также борьбы с шумом. В Канаде и США, Германии и Франции, а также Японии идут активные поиски по развитию и совершенствованию его использования.
Будущее
Явные преимущества, которые имеет поршневой и роторный двигатель Стирлинга, заключающиеся в большом ресурсе работы, применении разного топлива, бесшумности и малой токсичности, делают его очень перспективным на фоне мотора внутреннего сгорания. Однако с учетом того, что ДВС на протяжении всего времени совершенствовали, он не может быть легко смещен. Так или иначе, именно такой двигатель сегодня занимает лидирующие позиции, и сдавать их в ближайшее время не намерен.
ЖРД открытого цикла — Википедия
Материал из Википедии — свободной энциклопедии
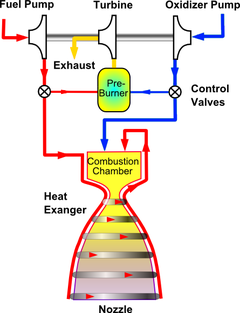
«ЖРД c открытым циклом», «ЖРД без дожигания» (англ. Gas-generator cycle) — схема работы жидкостного ракетного двигателя, использующего два жидких компонента — горючее и окислитель. Часть топлива сжигается в газогенераторе и полученный горячий газ — часто называемый генераторным газом — используется для приведения в действие топливных насосов, после чего сбрасывается. Открытую схему ЖРД также называют газогенераторным циклом. В некоторых случаях, для привода турбины используется отдельное топливо, в частности, однокомпонентное, такое, как пероксид водорода, разлагаемое в каталитическом газогенераторе. Так получают генераторный газ двигатели давней разработки, впрочем, некоторые из них, такие, как РД-107, РД-108, весьма активно используются и сейчас. Также использовались твердотопливные газогенераторы с шашкой специальной формы, обеспечивающей постоянство поверхности горения (а, значит, и частоты вращения турбонасосного агрегата) во время работы. По такой схеме работал пусковой газогенератор с пороховой шашкой для раскрутки турбины и запуска основного газогенератора двигателя ЖРД советской ракеты 8К14 («Скад») и аналогичных ей.
Существует определенные преимущества открытого цикла по сравнению c ЖРД закрытого цикла. В данном случае нет необходимости обеспечивать подачу полученного генераторного газа в камеру сгорания, находящуюся под высоким давлением, что позволяет турбине производить больше энергии и увеличить давление в камере сгорания, таким образом увеличивая удельный импульс или эффективность. Также это уменьшает износ турбины, увеличивает её надежность, сокращает стоимость производства и увеличивает время службы турбины, что особенно важно в случае применения на многоразовой системе.
Основным недостатком является потеря эффективности в силу неиспользованного для создания тяги топлива, хотя эта потеря эффективности может быть скомпенсирована созданием двигателей с более высоким давлением в камере сгорания, что приводит к росту практического КПД. Отработанный генераторный газ часто сбрасывается через отдельное сопло, создавая тем самым дополнительную тягу. Но даже в этом случае, открытый цикл имеет тенденцию быть менее эффективным по сравнению с закрытым циклом с дожиганием генераторного газа (англ. staged combustion cycle, «цикл поэтапного сгорания»).
Как и в большинстве криогенных ЖРД, при открытом цикле часть топлива используется для охлаждения сопла, стенок камеры сгорания и газогенератора. Существующие в настоящее время конструкционные материалы не в состоянии противостоять экстремальным температурам при сжигании топлива и окислителя. Используя современные технологии и материалы, охлаждение позволяет использовать ЖРД в течение более продолжительного времени. Без охлаждения камер сгорания и сопел, двигатель подвергся бы катастрофическому разрушению.[1]
Последними примерами разработанных двигателей открытого цикла являются ЖРД Мерлин на РН Фалькон 9 (SpaceX) и ЖРД Вулкан на РН Ариан 5 (ЕКА).
- ↑ Жидкий водород в качестве ракетного топлива, 1945-1959, Охлаждение ЖРД (en)
Газотурбинный двигатель — Википедия
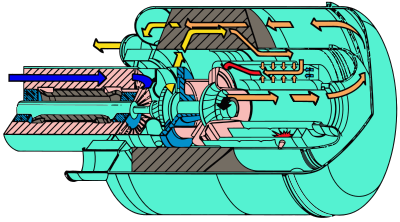
Газотурбинный двигатель (ГТД) — это воздушный двигатель, в котором воздух сжимается нагнетателем перед сжиганием в нём топлива, а нагнетатель приводится газовой турбиной, использующей энергию нагретых таким образом газов. Двигатель внутреннего сгорания с термодинамическим циклом Брайтона.
То есть сжатый воздух из компрессора поступает в камеру сгорания, куда подаётся топливо, которое, сгорая, образует газообразные продукты с большей энергией. Затем в газовой турбине часть энергии продуктов сгорания преобразуется во вращение турбины, которая расходуется на сжатие воздуха в компрессоре. Остальная часть энергии может передаваться на приводимый агрегат или использоваться для создания реактивной тяги. Эта часть работы двигателя считается полезной. Газотурбинные двигатели имеют большую удельную мощность до 6 кВт/кг.
В качестве топлива используется разнообразное горючее. Например: бензин, керосин, дизельное топливо, мазут, природный газ, судовое топливо, водяной газ, спирт и измельчённый уголь.
Одну из простейших конструкций газотурбинного двигателя, для понятия его работы, можно представить как вал, на котором находится два диска с лопатками, первый диск — компрессора, второй — турбины, в промежутке между ними установлена камера сгорания.
Простейшая схема газотурбинного двигателя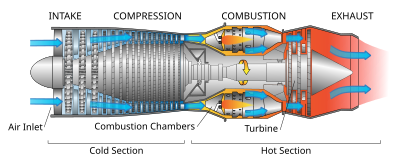
Принцип работы газотурбинного двигателя:
- всасывание и сжатие воздуха в осевом компрессоре, подача его в камеру сгорания;
- смешение сжатого воздуха с топливом для образования топливо-воздушной смеси (ТВС) и сгорание этой смеси;
- расширение газов из-за её нагрева при сгорании топливо-воздушной смеси, что формирует вектор давления газа, направленный в сторону меньшего сопротивления (в направлении лопаток турбины), передача энергии (давления) газа лопатками турбины на диск или вал, в котором эти лопатки закреплены;
- привод во вращение диска турбины и, вследствие этого, передача крутящего момента по валу с диска турбины на диск компрессора.[1]
Увеличение количества подаваемого топлива (добавление «газа») вызывает генерирование большего количества газов высокого давления, что, в свою очередь, ведёт к увеличению числа оборотов турбины и диска(ов) компрессора и, вследствие этого, увеличению количества нагнетаемого воздуха и его давления, что позволяет подать в камеру сгорания и сжечь больше топлива. Количество топливо-воздушной смеси зависит напрямую от количества воздуха, поданного в камеру сгорания. Увеличение количества ТВС (топливо-воздушной смеси) приведёт к увеличению давления в камере сгорания и температуры газов на выходе из камеры сгорания и, вследствие этого, позволяет создать бо́льшую энергию выбрасываемых газов, направленную для вращения турбины и повышения реактивной силы.
Как и во всех циклических тепловых двигателях, чем выше температура сгорания, тем выше топливный коэффициент полезного действия (если точнее, чем выше разница между «нагревателем» и «охладителем»). Сдерживающим фактором является способность стали, никеля, керамики или других материалов, из которых состоит двигатель, выдерживать температуру и давление. Значительная часть инженерных разработок направлена на то, чтобы отводить тепло от частей турбины. Большинство турбин также пытается рекуперировать тепло выхлопных газов, которое, в противном случае, теряется впустую. Рекуператоры — это теплообменники, которые передают тепло выхлопных газов сжатому воздуху перед сгоранием. Также существует и другой способ утилизации тепла остаточных газов — подача в паровой котёл-утилизатор. Генерируемый котлом пар может быть передан паровой турбине для выработки дополнительной энергии в комбинированном цикле на парогазовой установке, либо использоваться для нужд отопления и ГВС в комбинированном производстве тепла и электроэнергии (когенерация) на газотурбинной ТЭЦ.
Чем меньше двигатель, тем выше должна быть частота вращения вала(ов), необходимая для поддержания максимальной линейной скорости лопаток, так как длина окружности (путь, проходимый лопатками за один оборот), прямо зависит от радиуса ротора. Максимальная скорость турбинных лопаток определяет максимальное давление, которое может быть достигнуто, что приводит к получению максимальной мощности, независимо от размера двигателя. Вал реактивного двигателя вращается с частотой около 10000 об/мин и микротурбина — с частотой около 100000 об/мин.[2][3]
Для дальнейшего развития авиационных и газотурбинных двигателей рационально применять новые разработки в области высокопрочных и жаропрочных материалов для возможности повышения температуры и давления. Применения новых типов камер сгорания, систем охлаждения, уменьшения числа и массы деталей и двигателя в целом возможно в прогрессе применение альтернативных видов топлива, изменение самого представления конструкции двигателя.
Газотурбинная установка (ГТУ) с замкнутым циклом[править | править код]
В ГТУ с замкнутым циклом рабочий газ циркулирует без контакта с окружающей средой. Нагрев (перед турбиной) и охлаждение (перед компрессором) газа производится в теплообменниках. Такая система позволяет использовать любой источник тепла (например, газоохлаждаемый ядерный реактор). Если в качестве источника тепла используется сгорание топлива, то такое устройство называют двигателем внешнего сгорания. На практике ГТУ с замкнутым циклом используются редко.
Газотурбинная установка (ГТУ) с внешним сгоранием[править | править код]
Большинство ГТУ представляют собой двигатели внутреннего сгорания, но также возможно построить ГТУ внешнего сгорания, которая, фактически, является газотурбинной версией теплового двигателя.[источник не указан 3006 дней]
При внешнем сгорании в качестве топлива используется пылевидный уголь или мелкоистолчённая биомасса (например, опилки). Внешнее сжигание газа используется как непосредственно, так и косвенно. В прямой системе сквозь турбину проходят продукты сгорания. В косвенной системе используется теплообменник, и через турбину проходит чистый воздух. Тепловой КПД ниже в системе внешнего сгорания косвенного типа, однако лопасти не подвергаются воздействию продуктов сгорания.
Одновальные и многовальные газотурбинные двигатели[править | править код]
Простейший газотурбинный двигатель имеет только один вал, куда устанавливается турбина, которая приводит во вращение компрессор и одновременно является источником полезной мощности. Это накладывает ограничение на режимы работы двигателя.
Иногда двигатель выполняется многовальным. В этом случае имеется несколько последовательно стоящих турбин, каждая из которых приводит свой вал. Турбина высокого давления (первая после камеры сгорания) всегда приводит в движение компрессор двигателя, а последующие могут приводить как внешнюю нагрузку (винты вертолёта[4] или корабля, мощные электрогенераторы и так далее), так и дополнительные каскады компрессора самого двигателя, расположенные перед основным. Разбиение компрессора на каскады (каскад низкого давления, каскад высокого давления — КНД и КВД соответственно[5], иногда между ними помещается каскад среднего давления, КСД, как, например, в двигателе НК-32 самолёта Ту-160) позволяет избежать помпажа на частичных режимах.
Также преимущество многовального двигателя в том, что каждая турбина работает при оптимальной скорости вращения и нагрузке. При нагрузке, приводимой от вала одновального двигателя, была бы очень плохая приёмистость двигателя, то есть способность к быстрой раскрутке, так как турбине требуется поставлять мощность и для обеспечения двигателя большим количеством воздуха (мощность ограничивается количеством воздуха), и для разгона нагрузки. При двухвальной схеме лёгкий ротор высокого давления быстро выходит на режим, обеспечивая двигатель воздухом, а турбину низкого давления — большим количеством газов для разгона. Также есть возможность использовать менее мощный стартёр для разгона при пуске только ротора высокого давления.
Система запуска[править | править код]
Для запуска ГТД нужно раскрутить его ротор до определённых оборотов, чтобы компрессор начал подавать достаточное количество воздуха (в отличие от объёмных компрессоров, подача инерционных (динамических) компрессоров квадратично зависит от частоты вращения и поэтому на малых оборотах практически отсутствует), и поджечь подаваемое в камеру сгорания топливо. Со второй задачей справляются свечи зажигания, зачастую установленные на специальных пусковых форсунках, а раскрутка выполняется стартером той или иной конструкции:
- электростартер, зачастую являющийся стартёр-генератором, то есть после запуска переключающимся в режим генератора постоянного тока 27 вольт. Таковы, например, ГС-24 вспомогательного двигателя ТА-6Б или СТГ-18 турбовинтового двигателя АИ-24 самолёта Ан-24;
- воздушный турбостартер (ВТС) — небольшая воздушная турбина, получающая воздух от системы отбора (от ВСУ или соседнего работающего двигателя) или наземной установки воздушного запуска (УВЗ). Такие стартёры стоят на двигателях Д-30КП самолёта Ил-76, ТВ3-117 вертолётов Ми-8 и Ми-24 и многих других;
- турбостартер (ТС) — небольшой турбовальный двигатель, рассчитанный только на раскрутку ротора основного двигателя, на котором он и установлен. Такие стартёры стоят, например, на двигателе АИ-25ТЛ учебно-тренировочного самолёта L-39 и НК-12МВ дальнего бомбардировщика Ту-95. Сам ТС имеет электрозапуск.[6]
Турбореактивный двигатель[править | править код]
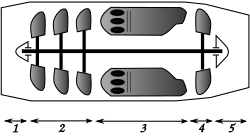
В полёте поток воздуха тормозится во входном устройстве перед компрессором, в результате чего его температура и давление повышается. На земле во входном устройстве воздух ускоряется, его температура и давление снижаются.
Проходя через компрессор, воздух сжимается, его давление повышается в 10—45 раз, возрастает его температура. Компрессоры газотурбинных двигателей делятся на осевые и центробежные. В наши дни в двигателях наиболее распространены многоступенчатые осевые компрессоры. Центробежные компрессоры, как правило, применяются в малогабаритных силовых установках.
Далее сжатый воздух попадает в камеру сгорания, в так называемые жаровые трубы, либо в кольцевую камеру сгорания, которая не состоит из отдельных труб, а является цельным кольцевым элементом. В наши дни кольцевые камеры сгорания являются наиболее распространёнными. Трубчатые камеры сгорания используются гораздо реже, в основном на военных самолётах. Воздух на входе в камеру сгорания разделяется на первичный, вторичный и третичный. Первичный воздух поступает в камеру сгорания через специальное окно в передней части, по центру которого расположен фланец крепления форсунки, и участвует непосредственно в окислении (сгорании) топлива (формировании топливо-воздушной смеси). Вторичный воздух поступает в камеру сгорания сквозь отверстия в стенках жаровой трубы, охлаждая, придавая форму факелу и не участвуя в горении. Третичный воздух подаётся в камеру сгорания уже на выходе из неё, для выравнивания поля температур. При работе двигателя в передней части жаровой трубы всегда вращается вихрь раскалённого газа (что обусловлено специальной формой передней части жаровой трубы), постоянно поджигающего формируемую топливовоздушную смесь, происходит сгорание топлива (керосина, газа), поступающего через форсунки в парообразном состоянии.
Газовоздушная смесь расширяется и часть её энергии преобразуется в турбине через рабочие лопатки в механическую энергию вращения основного вала. Эта энергия расходуется, в первую очередь, на работу компрессора, а также используется для привода агрегатов двигателя (топливных подкачивающих насосов, масляных насосов и т. п.) и привода электрогенераторов, обеспечивающих энергией различные бортовые системы.
Основная часть энергии расширяющейся газовоздушной смеси идёт на ускорение газового потока в сопле и создание реактивной тяги.
Чем выше температура сгорания, тем выше КПД двигателя. Для предупреждения разрушения деталей двигателя для их изготовления используют жаропрочные сплавы и термобарьерные покрытия. А также применяется система охлаждения воздухом, отбираемым от средних ступеней компрессора.
Турбореактивный двигатель с форсажной камерой[править | править код]
Турбореактивный двигатель с форсажной камерой (ТРДФ) — модификация ТРД, применяемая в основном на сверхзвуковых самолётах. Между турбиной и соплом устанавливается дополнительная форсажная камера, в которой сжигается дополнительное горючее. В результате происходит увеличение тяги (форсаж) до 50 %, но расход топлива резко возрастает. Двигатели с форсажной камерой, как правило, не используются в коммерческой авиации по причине их низкой экономичности.
Двухконтурный турбореактивный двигатель[править | править код]
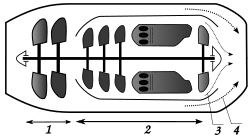
В турбореактивном двухконтурном двигателе (ТРДД) воздушный поток попадает в компрессор низкого давления, после чего часть потока проходит по обычной схеме через турбокомпрессор, а остальная часть (холодная) проходит через внешний контур и выбрасывается без сгорания, создавая дополнительную тягу. В результате снижается температура выходного газа, снижается расход топлива и уменьшается шум двигателя. Отношение количества воздуха, прошедшего через внешний контур, к количеству прошедшего через внутренний контур воздуха называется степенью двухконтурности (m). При степени двухконтурности <4 потоки контуров на выходе, как правило, смешиваются и выбрасываются через общее сопло, если m > 4 — потоки выбрасываются раздельно, так как из-за значительной разности давлений и скоростей смешение затруднительно. Применение второго контура в двигателях для военной авиации позволяет охлаждать горячие части двигателя, это позволяет увеличивать температуру газов перед турбиной, что способствует дополнительному повышению тяги.
Двигатели с малой степенью двухконтурности (m < 2) применяются для сверхзвуковых самолётов, двигатели с m > 2 для дозвуковых пассажирских и транспортных самолётов.
Турбовентиляторный двигатель[править | править код]
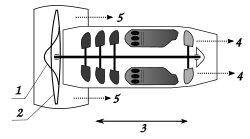
Турбовентиляторный реактивный двигатель (ТВРД) — это ТРДД со степенью двухконтурности m=2—10. Здесь компрессор низкого давления преобразуется в вентилятор, отличающийся от компрессора меньшим числом ступеней и большим диаметром, и горячая струя практически не смешивается с холодной. Применяется в гражданской авиации, двигатель имеет большой назначенный ресурс и малый удельный расход топлива на дозвуковых скоростях.
Турбовинтовентиляторный двигатель[править | править код]
Дальнейшим развитием ТВРД с увеличением степени двухконтурности m=20—90 является турбовинтовентиляторный двигатель (ТВВД). В отличие от турбовинтового двигателя, лопасти двигателя ТВВД имеют саблевидную форму, что позволяет перенаправить часть воздушного потока в компрессор и повысить давление на входе компрессора. Такой двигатель получил название винтовентилятор и может быть как открытым, так и закапотированным кольцевым обтекателем. Второе отличие — винтовентилятор приводится от турбины не напрямую, а, как винт, через редуктор. Двигатель наиболее экономичен, но при этом крейсерская скорость полёта ЛА, с такими типами двигателей, обычно не превышает 550 км/ч, имеются более сильные вибрации и «шумовое загрязнение».
Пример ТВВД — Д-27 грузового самолёта Ан-70.
Турбовинтовой двигатель[править | править код]
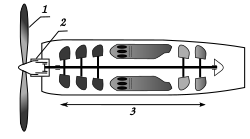
В турбовинтовом двигателе (ТВД) основное тяговое усилие обеспечивает воздушный винт, соединённый через редуктор с валом турбокомпрессора.[7] Для этого используется турбина с увеличенным числом ступеней, так что расширение газа в турбине происходит почти полностью и только 10—15 % тяги обеспечивается за счёт газовой струи.
Турбовинтовые двигатели гораздо более экономичны на малых скоростях полёта и широко используются для самолётов, имеющих большую грузоподъёмность и дальность полёта — например, Ан-12, Ан-22, C-130. Крейсерская скорость самолётов, оснащённых ТВД, 500—700 км/ч.
Вспомогательная силовая установка (ВСУ)[править | править код]
ВСУ — небольшой газотурбинный двигатель, являющийся автономным источником энергии на борту. Простейшие ВСУ могут выдавать только сжатый воздух, отбираемый от компрессора турбины, который используется для запуска маршевых (основных) двигателей, либо для работы системы кондиционирования на земле (пример, ВСУ типа АИ-9, применяемая на вертолётах и самолёте Як-40). Более сложные ВСУ, помимо источника сжатого воздуха, выдают электрический ток в бортовую сеть, то есть являются полноценным автономным энергоузлом, обеспечивающем нормальное функционирование всех бортовых систем самолёта без запуска основных двигателей, а также при отсутствии наземных аэродромных источников энергии. Такова, например, ВСУ ТА-12 самолётов Ан-124[8], Ту-95МС, Ту-204, Ан-74 и других.
Турбовальный двигатель[править | править код]
Такой двигатель чаще всего имеет свободную турбину. Вся турбина поделена на две части, между собой механически несвязанные. Связь между ними только газодинамическая. Газовый поток, вращая первую турбину, отдает часть своей мощности для вращения компрессора и далее, вращая вторую, тем самым через вал этой (второй) турбины приводит в действие полезные агрегаты. Реактивное сопло на турбовальном двигателе отсутствует. Выходное устройство для отработанных газов соплом не является и тяги не создаёт.
Выходной вал ТВаД, с которого снимается вся полезная мощность, может быть направлен как назад, через канал выходного устройства, так и вперед, либо через полый вал турбокомпрессора, либо через редуктор вне корпуса двигателя.
Редуктор — непременная принадлежность турбовального двигателя. Скорость вращения как ротора турбокомпрессора, так и ротора свободной турбины велика настолько, что это вращение не может быть напрямую передано на приводимые агрегаты. Они просто не смогут выполнять свои функции и даже могут разрушиться. Поэтому между свободной турбиной и полезным агрегатом обязательно ставится редуктор для снижения частоты вращения приводного вала.
Компрессор у ТВаД может быть осевым (если двигатель мощный) либо центробежным. Часто компрессор бывает и смешанным по конструкции, в нём есть как осевые, так и центробежные ступени. В остальном принцип работы этого двигателя такой же, как и у ТРД.
Основное применение турбовальный двигатель находит в авиации, по большей части, на вертолётах. Полезная нагрузка в этом случае — несущий винт вертолёта. Известным примером могут служить широко распространённые вертолёты Ми-8 и Ми-24 с двигателями ТВ2-117 и ТВ3-117.
Турбостартёр[править | править код]
ТС — агрегат, устанавливаемый на газотурбинном двигателе и предназначенный для его раскрутки при запуске.
Такие устройства представляют собой миниатюрный, простой по конструкции турбовальный двигатель, свободная турбина которого раскручивает ротор основного двигателя при его запуске. В качестве примера: турбостартёр ТС-21, используемый на двигателе АЛ-21Ф-3, который устанавливается на самолёты типа Су-24[9], или ТС-12, устанавливаемый на авиационные двигатели НК-12 самолётов Ту-95 и Ту-142. ТС-12 имеет одноступенчатый центробежный компрессор, двухступенчатую осевую турбину привода компрессора и двухступенчатую свободную турбину. Номинальные обороты ротора компрессора в начале запуска двигателя — 27 тысяч мин−1, по мере раскрутки ротора НК-12 за счёт роста оборотов свободной турбины ТС-12 противодавление за турбиной компрессора падает и обороты возрастают до 30 тысяч мин−1.
Турбостартёр ГТДЭ-117 двигателя АЛ-31Ф также выполнен со свободной турбиной, а стартёр С-300М двигателя АМ-3, стоявшего на самолётах Ту-16, Ту-104 и М-4 — одновальный и раскручивает ротор двигателя через гидромуфту.[10]
Судовые установки[править | править код]
Используются в судовой промышленности для снижения веса. General Electric LM2500 и LM6000 — характерные модели этого типа машин.
Суда, использующие турбовальные газотурбинные двигатели называют газотурбоходами. Они являются разновидностью теплохода. Это чаще всего суда на подводных крыльях, у которых гребной винт приводит в движение турбовальный двигатель механически через редуктор или электрически через генератор, который он вращает. Либо это суда на воздушной подушке, которая создаётся при помощи ГТД.
Например, газотурбоход «Циклон-М» с 2 газотурбинными двигателями ДО37. Пассажирских газотурбоходов за российскую историю было всего два. Последнее очень перспективное судно «Циклон-М» появилось в 1986 году. Более таких судов не строили. В военной сфере в этом плане дела обстоят несколько лучше. Примером является десантный корабль «Зубр», самое большое в мире судно на воздушной подушке.
Железнодорожные установки[править | править код]
Локомотивы, на которых стоят турбовальные газотурбинные двигатели, называются газотурбовозами (разновидность тепловоза). На них используется электрическая передача. ГТД вращает электрогенератор, а вырабатываемый им ток, в свою очередь, питает электродвигатели, приводящие локомотив в движение. В 1960-е годы в СССР проходили довольно успешную опытную эксплуатацию три газотурбовоза. Два пассажирских и один грузовой. Однако они не выдержали соревнования с электровозами и в начале 1970-х годов проект был свёрнут. Но в 2007 году по инициативе ОАО «РЖД» был изготовлен опытный образец грузового газотурбовоза, работающий на сжиженном природном газе. ГТ1 успешно прошёл испытания, позднее был построен второй газотурбовоз, с той же силовой установкой, но на другой ходовой части, машины эксплуатируются.
Перекачка природного газа[править | править код]
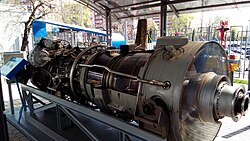
Принцип работы газоперекачивающей установки практически не отличается от турбовинтовых двигателей, ТВаД используются здесь в качестве привода мощных насосов, а в качестве топлива используется тот же самый газ, который они перекачивают. В отечественной промышленности для этих целей широко применяются двигатели, созданные на базе авиационных — НК-12 (НК-12СТ)[11], НК-32 (НК-36СТ), так как на них можно использовать детали авиадвигателей, выработавшие свой лётный ресурс.
Электростанции[править | править код]
Турбовальный газотурбинный двигатель может использоваться для привода электрогенератора на электростанциях, основу которой составляют один или несколько таких двигателей. Такая электростанция может иметь электрическую мощность от двадцати киловатт до сотен мегаватт.
Однако, газотурбинный двигатель, помимо вращения, также производит большое количество тепла, которое также может быть использовано для производства электроэнергии или теплоснабжения, поэтому наиболее эффективно его применение совместно с котлом-утилизатором. Полученный в котле-утилизаторе пар подаётся в паротурбинную установку, в таком случае вся установка в целом называется парогазовой, либо подаётся в сетевой подогреватель для использования в теплофикации, в таком случае установка называется газотурбинной ТЭЦ.
Парогазовая установка является одним из самых распространённых и эффективных источников электроэнергии, её КПД выше, чем у отдельных паросиловых и газотурбинных установок.
Танкостроение[править | править код]
Первые исследования в области применения газовой турбины в танковых двигателях проводились в Германии Управлением вооружённых сухопутных сил начиная с середины 1944 года. Первым массовым танком с газотурбинным двигателем стал С-танк.
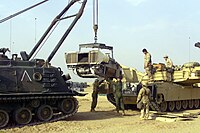
Турбовальные двигатели (ТВаД) установлены на советском танке Т-80 (двигатель ГТД-1000Т) и американском М1 Абрамс. Газотурбинные двигатели, устанавливаемые на танках, имеют при схожих с дизельными размерах гораздо бо́льшую мощность, меньший вес и меньшую шумность, меньшую дымность выхлопа. Также ТВаД лучше удовлетворяет требованиям многотопливности, гораздо легче запускается, — оперативная готовность танка с ГТД, то есть запуск двигателя и последующий вход в рабочий режим всех его систем, занимает несколько минут, что для танка с дизельным двигателем в принципе невозможно, а в зимних условиях при низких температурах дизелю требуется достаточно длительный предпусковой прогрев, который не требуется ТВаД. Из-за отсутствия жёсткой механической связи турбины и трансмиссии на застрявшем или просто упёршемся в препятствие танке двигатель не глохнет. В случае попадания воды в двигатель (утоплении танка) достаточно выполнить так называемую холодную прокрутку ГТД для удаления воды из газовоздушного тракта и после этого двигатель можно запускать — на танке с дизельным двигателем в аналогичной ситуации происходит гидроудар, ломающий детали цилиндро-поршневой группы и непременно требующий замены двигателя.
Однако из-за низкого КПД газотурбинных двигателей, установленных на тихоходных (в отличие от самолётов) транспортных средствах, требуется гораздо большее количество возимого топлива для сравнимого с дизельным двигателем километрового запаса хода. Именно из-за расхода топлива, невзирая на все достоинства, танки типа Т-80 поэтапно выводятся из эксплуатации. Неоднозначным оказался опыт эксплуатации танковых ТВаД М1 Абрамс в условиях высокой запылённости (например в песчаных пустынях). В отличие от него, Т-80 благополучно может эксплуатироваться в условиях высокой запылённости, — конструктивно хорошо продуманная система очистки поступающего в двигатель воздуха на Т-80 надёжно защищает ГТД от песка и пыли. «Абрамсы», напротив, «задохнулись» — во время двух кампаний против Ирака при прохождении пустынь довольно много «Абрамсов» встали, так как их двигатели забились песком[источник не указан 709 дней].
Автостроение[править | править код]
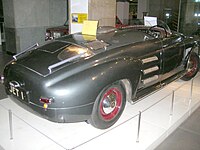
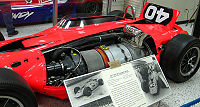
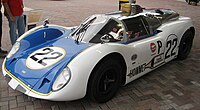
Множество экспериментов проводилось с автомобилями, оснащёнными газовыми турбинами.
В 1950 году дизайнер Ф. Р. Белл и главный инженер Морис Вилкс в британской компании Rover Company анонсировали первый автомобиль с приводом от газотурбинного двигателя. Двухместный JET1 имел двигатель, расположенный позади сидений, решётки воздухозаборника по обеим сторонам машины, и выхлопные отверстия на верхней части хвоста. В ходе испытаний автомобиль достиг максимальной скорости 140 км/ч, на скорости турбины 50000 об/мин. Автомобиль работал на бензине, парафиновом или дизельном маслах, но проблемы с потреблением топлива оказались непреодолимыми для производства автомобилей. В настоящее время он выставлен в лондонском Музее науки.
Команды Rover и British Racing Motors (Формула-1) объединили усилия для создания Rover-BRM, автомобиля с приводом от газовых турбин, который принял участие в гонке 24 часа Ле-Мана 1963 года, управляемого Грэмом Хиллом и Гитнером Ричи. Этот автомобиль показал среднюю скорость 173 км/ч, максимальную — 229 км/ч.
Американские компании Ray Heppenstall, Howmet Corporation и McKee Engineering объединились для совместной разработки собственных газотурбинных спортивных автомобилей в 1968 году, Howmet TX приняла участие в нескольких американских и европейских гонках, в том числе завоевав две победы, а также принимала участие в гонке 24 часа Ле-Мана 1968 года. Автомобили использовали газовые турбины Continental Motors Company, благодаря которым, в конечном итоге, ФИА было установлено шесть посадочных скоростей для машин с приводом от турбин.
На гонках автомобилей с открытыми колёсами, революционное полноприводное авто 1967 года STP Oil Treatment Special с приводом от турбины, специально подобранной легендой гонок Эндрю Гранателли и управляемое Парнелли Джонсом, почти выиграло в гонке «Инди-500»; авто с турбиной STP компании Pratt & Whitney обгоняло почти на круг авто, шедшее вторым, когда у него неожиданно отказала коробка передач за три круга до финишной черты. В 1971 году глава компании Lotus Колин Чепмен представил авто Lotus 56B F1, с приводом от газовой турбины Pratt & Whitney. У Чепмена была репутация создателя машин-победителей, но он вынужден был отказаться от этого проекта из-за многочисленных проблем с инерционностью турбин (турболагом).
Оригинальная серия концептуальных авто General Motors Firebird была разработана для автовыставки Моторама 1953, 1956, 1959 годов, с приводом от газовых турбин.
Единственная серийная модель «семейного» газотурбинного автомобиля для использования на дорогах общего пользования была выпущена Chrysler в 1963—1964 года. Компания передала пятьдесят собранных вручную машин в кузовах итальянского ателье Ghia добровольцам, которые испытывали новинку в обычных дорожных условиях до января 1966 года. Эксперимент прошёл удачно, но компания, не располагавшая средствами для постройки нового моторного производства, отказалась от массового выпуска автомобиля с ГТД. После ужесточения экологических стандартов и взрывного роста цен на нефть компания, с трудом пережившая финансовый кризис, отказалась от продолжения разработок[12].[13]
В 1791 году английский изобретатель Джон Барбер получил патент за номером 1833, в котором описал первую газовую турбину.[14]
В 1892 году русский инженер П. Д. Кузьминский конструировал и построил первый в мире ГТД с газовой реверсивной турбиной радиального типа с 10 ступенями давления.[15] Турбина должна была работать на парогазовой смеси, которая получалась в созданной им же камере сгорания — «газопаророде».[16]
В 1906—1908 году русский инженер В. В. Кароводин сконструировал газовую турбину взрывного типа (турбину постоянного объёма).[17] Бескомпрессорный ГТД Кароводина с 4 камерами прерывистого сгорания и газовой турбиной при 10 000 об/мин развивал мощность 1,2 квт (1,6 л. с.).[18]
В 1909 году русский инженер Н. Герасимов запатентовал ГТД, использующийся для реактивного движения, то есть по сути — первый турбореактивный двигатель (привилегия № 21021, 1909 г.).[19][20][21]
В 1913 г., М. Н. Никольский спроектировал газотурбинный двигатель мощностью 120 кВт (160 л. с.), у которого было три ступени газовой турбины.[22][23]
Дальнейшие усовершенствования в конструкцию газотурбинных двигателей внесли В. И. Базаров (1923 г.), В. В. Уваров и Н. Р. Брилинг (1930—1936 гг.).[24][25]
В 1930-е годы огромный вклад в развитие газотурбинных технологий внесла группа конструкторов под руководством академика АН СССР А. М. Люльки. Главные работы конструктора касались турбореактивных двигателей с центробежным лопастным компрессором, которые стали основными для авиации.[26][27][28][29]
Как и у любого теплового двигателя, у ГТД есть множество параметров, которые необходимо контролировать для эксплуатации двигателя в безопасных, а по возможности и экономичных режимах. Измеряются с помощью приборов контроля.
- Обороты — контролируются для оценки режима работы двигателя и недопущения опасных режимов. У многовальных двигателей, как правило, контролируются обороты всех валов — например, на Як-42 для контроля оборотов всех трёх валов каждого двигателя Д-36 установлен трёхстрелочный тахометр ИТА-13[30], на Ан-72 и Ан-74, оснащённых такими же двигателями Д-36 — три двухстрелочных тахометра, два стоят на приборной доске пилотов и показывают один обороты роторов вентиляторов, второй обороты роторов ВД, третий установлен на пульте предполётной подготовки и показывает обороты роторов НД.
- Температура выходящих газов (ТВГ) — температура газов за турбиной двигателя, как правило, за последней ступенью[5], так как температура перед турбиной слишком высока для надёжного измерения. Температура газов показывает тепловую нагрузку на турбину и измеряется с помощью термопар. Также от термопар может работать автоматика, срезающая расход топлива или вовсе выключающая двигатель при превышении ТВГ — СОТ-1 на двигателе ТА-6[1], РТ-12 на двигателе НК-8 и так далее.
Конструкторы газотурбинных двигателей и основанные ими КБ[править | править код]
Турбореактивный двигатель — Википедия
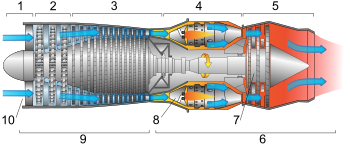
1. Забор воздуха
2. Компрессор низкого давления
3. Компрессор высокого давления
4. Камера сгорания
5. Расширение рабочего тела в турбине и сопле
6. Горячая зона
7. Турбина
8. Зона входа первичного воздуха в камеру сгорания
9. Холодная зона
10. Входное устройство
Турбореактивный двигатель (ТРД, англоязычный термин — turbojet engine) — воздушно-реактивный двигатель (ВРД), в котором сжатие рабочего тела на входе в камеру сгорания и высокое значение расхода воздуха через двигатель достигается за счёт совместного действия встречного потока воздуха и компрессора, размещённого в тракте ТРД сразу после входного устройства, перед камерой сгорания.
В 1791 году английский изобретатель Джон Барбер предложил идею коловратного двигателя с поршневым компрессором, камерой сгорания и газовой турбиной. В 1909 году русский изобретатель Н. В. Герасимов запатентовал схему газотурбинного двигателя для создания реактивной тяги (турбореактивного двигателя)[1][2][3]. Патент на использование газовой турбины для движения самолёта получен в 1921 году французским инженером Максимом Гийомом[fr].
Первый образец турбореактивного двигателя продемонстрировал английский инженер Фрэнк Уиттл 12 апреля 1937 года и созданная им небольшая частная фирма Power Jets[en]. Он основывался на теоретических работах Алана Гриффита[en].
Первое полезное применение турбореактивного двигателя произошло в Германии на самолёте Heinkel He 178 с ТРД HeS 3[en]. ТРД разработан Хансом фон Охайном почти одновременно с Уиттлом — первый пуск в сентябре 1937 года, изготовлялся фирмой Heinkel-Hirth Motorenbau. Лётчик Эрих Варзиц совершил первый полёт 27 августа 1939 года.
Компрессор втягивает воздух, сжимает его и направляет в камеру сгорания. В ней сжатый воздух смешивается с топливом, воспламеняется и расширяется. Расширенный газ заставляет вращаться турбину, которая расположена на одном валу с компрессором. Остальная часть энергии перемещается в сужающееся сопло. В результате направленного истечения газа из сопла на двигатель действует реактивная тяга. При горении топлива воздух, служащий рабочим телом, нагревается до 1500-2000 градусов цельсия.
Ключевые характеристики ТРД следующие:
- Создаваемая двигателем тяга.
- Удельный расход топлива (масса топлива, потребляемая за единицу времени для создания единицы тяги/мощности)
- Расход воздуха (масса воздуха, проходящего через каждое из сечений двигателя за единицу времени)
- Степень повышения полного давления в компрессоре
- Температура газа на выходе из камеры сгорания.
- Масса и габариты.
Степень повышения полного давления в компрессоре является одним из важнейших параметров ТРД, поскольку от него зависит эффективный КПД двигателя. Если у первых образцов ТРД (Jumo-004) этот показатель составлял 3, то у современных он достигает 40 (General Electric GE90).
Для повышения газодинамической устойчивости компрессоров они выполняются двухкаскадными (НК-22) или трехкаскадными (НК-25). Каждый из каскадов работает со своей скоростью вращения и приводится в движение своим каскадом турбины. При этом вал 1-го каскада компрессора (низкого давления), вращаемого последним (самым низкооборотным) каскадом турбины, проходит внутри полого вала компрессора второго каскада (каскада высокого давления для двухкаскадного двигателя, каскада среднего давления для трехкаскадного). Каскады двигателя также именуют роторами низкого, среднего и высокого давления.
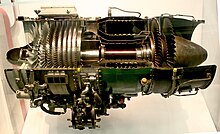
Камера сгорания большинства ТРД имеет кольцевую форму и вал турбина-компрессор проходит внутри кольца камеры. При поступлении в камеру сгорания воздух разделяется на 3 потока.
Первичный воздух — поступает через фронтальные отверстия в камере сгорания, тормозится перед форсунками и принимает непосредственное участие в формировании топливно-воздушной смеси. Непосредственно участвует в сгорании топлива. Топливо-воздушная смесь в зоне сгорания топлива в ВРД по своему составу близка к стехиометрической.
Вторичный воздух — поступает через боковые отверстия в средней части стенок камеры сгорания и служит для их охлаждения путём создания потока воздуха с гораздо более низкой температурой, чем в зоне горения.
Третичный воздух — поступает через специальные воздушные каналы в выходной части стенок камеры сгорания и служит для выравнивания поля температур рабочего тела перед турбиной.
Из камеры сгорания нагретое рабочее тело поступает на турбину, расширяется, приводя её в движение и отдавая ей часть своей энергии, а после неё расширяется в сопле и истекает из него, создавая реактивную тягу.
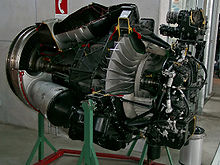
Благодаря компрессору ТРД (в отличие от ПВРД) может «трогать с места» и работать при низких скоростях полёта, что для двигателя самолёта является совершенно необходимым, при этом давление в тракте двигателя и расход воздуха обеспечиваются только за счёт компрессора.
При повышении скорости полёта давление в камере сгорания и расход рабочего тела растут за счёт роста напора встречного потока воздуха, который затормаживается во входном устройстве (так же, как в ПВРД) и поступает на вход низшего каскада компрессора под давлением более высоким, чем атмосферное, при этом повышается и тяга двигателя.
Диапазон скоростей, в котором ТРД эффективен, смещён в сторону меньших значений, по сравнению с ПВРД. Агрегат «турбина-компрессор», позволяющий создавать большой расход и высокую степень сжатия рабочего тела в области низких и средних скоростей полёта, является препятствием на пути повышения эффективности двигателя в зоне высоких скоростей:
- Температура, которую может выдерживать турбина, ограничена, что накладывает ограничение на количество тепловой энергии, подводимой к рабочему телу в камере сгорания, а это ведёт к уменьшению работы, производимой им при расширении.
- Повышение допустимой температуры рабочего тела на входе в турбину является одним из главных направлений совершенствования ТРД. Если для первых ТРД эта температура едва достигала 1000 К, то в современных двигателях она приближается к 2000 К. Это обеспечивается как за счёт применения особо жаропрочных материалов, из которых изготовляются лопатки и диски турбин, так и за счёт организации их охлаждения: воздух из средних ступеней компрессора (гораздо более холодный, чем продукты сгорания топлива) подается на турбину и проходит сквозь сложные каналы внутри турбинных лопаток.
- Турбина поглощает часть энергии рабочего тела перед поступлением его в сопло.
В результате максимальная скорость истечения реактивной струи у ТРД меньше, чем у ПВРД, что в соответствии с формулой для реактивной тяги ВРД на расчетном режиме, когда давление на срезе сопла равно давлению окружающей среды,[4]
где P{\displaystyle P} — сила тяги,
G{\displaystyle G} — секундный расход массы рабочего тела через двигатель,
c{\displaystyle c} — скорость истечения реактивной струи (относительно двигателя),
v{\displaystyle v} — скорость полёта,
ограничивает сверху диапазон скоростей, на которых ТРД эффективен, значениями M = 2,5 — 3 (M — число Маха). На этих и более высоких скоростях полёта торможение встречного потока воздуха создаёт степень повышения давления, измеряемую десятками единиц, такую же, или даже более высокую, чем у высоконапорных компрессоров, и ещё бо́льшее сжатие становится нежелательным, так как воздух при этом нагревается, а это ограничивает количество тепла, которое можно сообщить ему в камере сгорания. Таким образом, на высоких скоростях полёта (при M > 3) агрегат турбина-компрессор становится бесполезным, и даже контрпродуктивным, поскольку только создаёт дополнительное сопротивление в тракте двигателя, и в этих условиях более эффективными становятся прямоточные воздушно-реактивные двигатели.
Форсажная камера[править | править код]
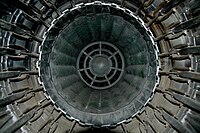

Хотя в ТРД имеет место избыток кислорода в камере сгорания, этот резерв мощности не удаётся реализовать напрямую — увеличением расхода горючего в камере — из-за ограничения температуры рабочего тела, поступающего на турбину. Этот резерв используется в двигателях, оборудованных форсажной камерой, расположенной между турбиной и соплом. В режиме форсажа в этой камере сжигается дополнительное количество горючего, внутренняя энергия рабочего тела перед расширением в сопле повышается, в результате чего скорость его истечения возрастает, и тяга двигателя увеличивается, в некоторых случаях, более, чем в 1,5 раза, что используется боевыми самолётами при полетах на высоких скоростях. В форсажной камере применяется стабилизатор, функция которого состоит в снижении скорости за ним до околонулевых значений, что обеспечивает стабильное горение топливной смеси. При форсаже значительно повышается расход топлива, ТРД с форсажной камерой практически не нашли применения в коммерческой авиации, за исключением самолётов Ту-144 и Конкорд, полеты которых уже прекратились.
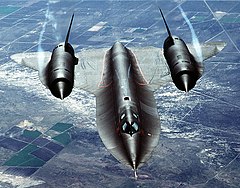
Гибридный ТРД / ПВРД[править | править код]
Турбопрямоточный двигатель J58В 1960-х годах в США был создан гибридный ТРД / ПВРД Pratt & Whitney J58, использовавшийся на стратегическом разведчике SR-71 Blackbird. До числа Маха М = 2,4 он работал как ТРД с форсажем, а на более высоких скоростях открывались каналы, по которым воздух из входного устройства поступал в форсажную камеру, минуя компрессор, камеру сгорания и турбину, подача топлива в форсажную камеру увеличивалась, и она начинала работать, как ПВРД. Такая схема работы позволяла расширить скоростной диапазон эффективной работы двигателя до М = 3,2. В то же время двигатель уступал по весовым характеристикам как ТРД, так и ПВРД, и широкого распространения этот опыт не получил.
Гибридный ТРД / РД[править | править код]
Двигатели этого типа при полете в атмосфере в качестве окислителя используют кислород из атмосферного воздуха, а при полете за пределами атмосферы в качестве окислителя используют жидкий кислород из топливных баков. Двигатели такого типа планировалось использовать в проекте HOTOL и намечено в проекте Skylon[5].
Регулируемые сопла[править | править код]
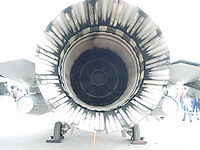
ТРД, скорость истечения реактивной струи в которых может быть как дозвуковой, так и сверхзвуковой на различных режимах работы двигателей, оборудуются регулируемыми соплами. Эти сопла состоят из продольных элементов, называемых створками, подвижных относительно друг друга и приводимых в движение специальным приводом, позволяющим по команде пилота или автоматической системы управления двигателем изменять геометрию сопла. При этом изменяются размеры критического (самого узкого) и выходного сечений сопла, что позволяет оптимизировать работу двигателя при полётах на разных скоростях и режимах работы двигателя.[1]
Область применения[править | править код]
ТРД наиболее активно развивались в качестве двигателей для всевозможных военных и коммерческих самолётов до 70-80-х годов XX века. В настоящее время ТРД потеряли значительную часть своей ниши в авиастроении, будучи вытесненными более экономичными двухконтурными ТРД (ТРДД).
- Образцы летательных аппаратов, оборудованных ТРД
-
Штурмовик Су-25 УБ с двумя ТРД Р-95Ш.
-
Сверхзвуковой авиалайнер Concorde с четырьмя ТРДФ Rolls-Royce Olympus 593.
Двухконтурный турбореактивный двигатель[править | править код]
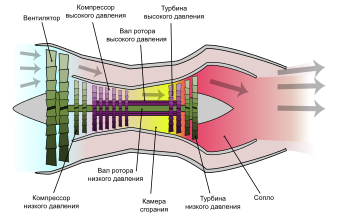
Впервые двухконтурный ТРД предложен создателем первого работоспособного ТРД Фрэнком Уитлом в начале 1930-х годов. Советский учёный и конструктор А. М. Люлька с 1937 года исследовал этот принцип и представил заявку на изобретение двухконтурного турбореактивного двигателя (авторское свидетельство 22 апреля 1941 года). Первые образцы ТРД с форсажными камерами созданы в Rolls-Royce во второй половине 1940-х годов, а Conway стал первым серийным.
В основе двухконтурных ТРД (далее — ТРДД) принцип вовлечения дополнительной массы воздуха в создание тяги, чтобы, прежде всего, увеличить КПД реактивного двигателя в плотной атмосфере. Эта часть воздуха нагнетается через внешний контур двигателя.
Пройдя через входное устройство, воздух попадает в компрессор низкого давления, иногда называемым вентилятором. После чего поток разделяется на две части: во внешний контур и, минуя камеру сгорания, далее в сопло, а другая часть во внутренний контур ТРД, где обычно последние ступени турбины приводят вентилятор.
Наиболее эффективные и мощные ТРДД делают трёхкаскадными, двух- и трёхвальными. К двум роторам внутреннего контура, называемого ещё газогенератором, добавляется ещё один, в котором вентилятор и последний каскад турбины соединены валом, расположенном внутри валов газогенератора.
Параметром ТРДД является степень двухконтурности — отношение расхода массы воздуха через внешний контур к расходу через внутренний. Повышение КПД достигается за счёт уменьшения разницы между скоростью истечения газов из сопла и скоростью самолёта за счёт увеличения расхода воздуха в двигателе, то есть увеличения площади входа в двигатель. Это ведёт к росту лобового сопротивления и массы.
ТРДД выполняют со смешением потоков контуров за турбиной и без смешения, с коротким внешним контуром. При смешении потоки смешиваются в особой камере и покидают двигатель через единое сопло с выровненной температурой. Наличие камеры смешения приводит к увеличению габаритов и массы двигателя, но увеличивает КПД и снижает шум, создаваемый струёй.
ТРДД, подобно ТРД, могут быть снабжены регулируемыми соплами и форсажными камерами для сверхзвуковых военных самолётов.
Управление вектором тяги (УВТ) / Отклонение вектора тяги (ОВТ)[править | править код]
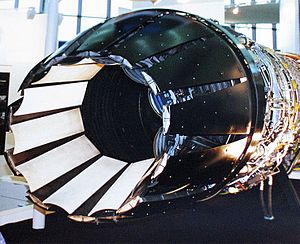
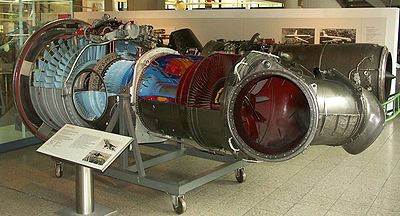
Специальные поворотные сопла на некоторых ТРДД позволяют отклонять истекающий из сопла поток рабочего тела относительно оси двигателя. ОВТ приводит к дополнительным потерям тяги двигателя за счёт выполнения дополнительной работы по повороту потока и усложняет управление самолётом. Но эти недостатки полностью компенсируются значительным повышением манёвренности и сокращением разбега самолёта при взлёте и пробега при посадке, вплоть до вертикальных взлёта и посадки. ОВТ используется исключительно в военной авиации.
ТРДД с высокой степенью двухконтурности / Турбовентиляторный двигатель[править | править код]
Порою в популярной литературе ТРДД с высокой степенью двухконтурности (выше 2) называют турбовентиляторными. В англоязычной литературе этот двигатель называется turbofan с добавлением уточнения high bypass (высокая двухконтурность), сокращённо — hbp. ТРДД с высокой степенью двухконтурности выполняются, как правило, без камеры смешения. По причине большого входного диаметра таких двигателей их сопло внешнего контура достаточно часто делают укороченным с целью снижения массы двигателя.
Область применения[править | править код]
Можно сказать, что с 1960-х и по сей день в самолётном авиадвигателестроении — эра ТРДД. ТРДД различных типов являются наиболее распространённым классом ВРД, используемых на самолётах, от высокоскоростных истребителей-перехватчиков с ТРДД с малой степенью до гигантских коммерческих и военно-транспортных самолётов с ТРДД с высокой степенью двухконтурности.
-
ТРДД с высокой степенью двухконтурности TF-39 (вид сзади)
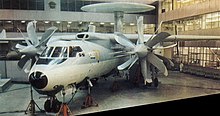
У винтовентиляторного двигателя поток холодного воздуха создаётся двумя соосными, вращающимися в противоположных направлениях, многолопастными саблевидными винтами, приводимыми в движение от турбины через редуктор. Степень двухконтурности таких двигателей достигает 90.
На сегодня известен лишь один серийный образец двигателя этого типа — Д-27 (ЗМКБ «Прогресс» им. академика А. Г. Ивченко, г. Запорожье, Украина.), использовавшийся на самолёте Як-44 с крейсерской скоростью полёта 670 км/ч, и на Ан-70 с крейсерской скоростью 750 км/ч.
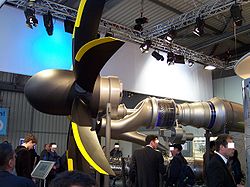
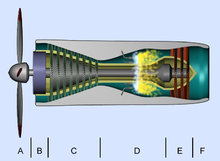
Турбовинтовые двигатели (ТВД) или турбовальные двигатели (ТВЛД)[источник не указан 184 дня] относятся к ВРД непрямой реакции.
Конструктивно ТВД схож с ТРД, в котором мощность, развиваемая последним каскадом турбины, передаётся на вал воздушного винта (обычно через редуктор). Этот двигатель не является, строго говоря, реактивным (реакция выхлопа турбины составляет не более 10 % его суммарной тяги), однако традиционно их относят к ВРД. Турбовинтовые двигатели используются в транспортной и гражданской авиации при полётах с крейсерскими скоростями 400—800 км/ч.
В ТВЛД газ, исходящий их камеры сгорания, направляется, во-первых, на турбину, приводящую в движение компрессор, а во-вторых, на турбину, связанную с приводным валом. Приводной вал механически соединяется с редуктором, приводящим в движение несущий винт. Таким образом, в ТВЛД связь ротора и выходного вала является чисто газодинамической. Такое техническое решение преимущественно применяется для силовых установок вертолетов из-за большого момента инерции несущего винта. В случае механической связи несущего винта с газогенератором запуск двигателя требует наличия стартера большой мощности.
Использует для нагрева воздуха ядерный реактор вместо сжигания керосина. Главным недостатком является сильное радиационное заражение использованного воздуха. Преимуществом является возможность длительного полета[6].
Газовый двигатель — Википедия
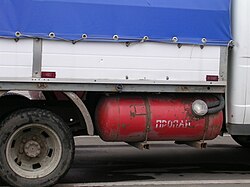
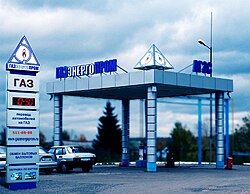
Газовый двигатель — двигатель внутреннего сгорания, использующий в качестве топлива сжиженные углеводородные газы (пропан-бутан) или природный газ (метан).
Газовый двигатель работает по тепловому циклу Отто, когда теплота подводится к рабочему телу при постоянном объёме. Отличие от бензиновых двигателей, работающих по этому циклу — более высокая степень сжатия (около 17-ти). Объясняется это тем, что используемые газы имеют более высокое октановое число, чем бензин.
В 1930-е—1940-е годы в связи с нехваткой бензина широкое распространение получили газогенераторные автомобили. На автомобиль устанавливался Газогенератор, из древесных чурок производился генераторный газ. В связи с низкой калорийностью газа (состав: окись углерода и водород) эти типы двигателей ушли в прошлое.
Как правило, газовые двигатели редко выпускаются серийно, за исключением применения их для специализированных задач в науке и технике.
Для работы на транспорте используются газовые двигатели, переоборудованные из традиционных бензиновых, а с недавнего времени — после развития в Европе соответствующих технологий — и из традиционных дизельных.
По причине более высокой степени сжатия дизельные двигатели более полно раскрывают потенциал газового двигателя по сравнению с бензиновыми «собратьями». Однако, переоборудование дизелей под использование газа имеет свои особенности. По причине того, что газ не воспламеняется, подобно дизельному топливу, при увеличении давления в цилиндре на такте сжатия, необходимо дооборудование дизелей системой зажигания (подобно бензиновым вариантам), либо использование в топливо-воздушной смеси части дизельного топлива в виде т. н. «запальной дозы» (от 30 до 50 % от всего количества топлива). В остальном, применение газа на дизельных двигателях все больше приобретает популярность, и обещает в ближайшие годы получить широкое распространение, как в виде газовых двигателей в «чистом виде», так и в универсальных газодизелях.
В целом, переоборудование двигателей внутреннего сгорания на транспорте под газовый двигатель существенно экономит средства их владельцам по причине более низкой отпускной цены на такой вид топлива.
Устройство и принцип работы газобаллонного автомобиля[править | править код]
Газозаправочная аппаратура на автомобиле Карбюратор-смесительАвтомобиль, оснащённый газобаллонным оборудованием (ГБО), использует в качестве топлива сжиженный нефтяной газ (смесь газов «пропан-бутан») или сжатый природный газ (метан).
На автомобиле сжиженная пропан-бутановая смесь находится в баллонах, установленных на раме, под полом салона автобуса или в багажнике легкового автомобиля. Сжиженный газ находится в баллоне под давлением 16 атмосфер (баллон рассчитан на максимальное давление 25 атмосфер).
На баллоны для сжиженного газа устанавливается специальный мультиклапан, через который производится заправка баллона и отбор газа в топливную систему двигателя. Мультиклапан является важным компонентом газобаллонного оборудования, обеспечивающим его безопасное использование. Он включает в себя[1]:
- Заправочный и расходный вентиль
- Указатель уровня газа в баллоне. Представляет собой поплавок на рычаге, находящийся внутри баллона, и связанный с ним стрелочный индикатор либо электронную схему, передающую информацию о положении поплавка на индикатор внутри салона автомобиля
- Обратный клапан в заправочной магистрали, предотвращающий вытекание газа через неё
- Скоростной клапан в расходной магистрали, перекрывающий подачу газа при превышении его расходом некоторого порогового значения. Порог подобран так, чтобы клапан закрывался только при разрыве расходной магистрали (предотвращая, таким образом, сильную утечку газа), и оставался открытым при обычном уровне расхода газа.
- Стопорный клапан, предотвращающий наполнение баллона газом более чем на 80-90 %%. Клапан находится в заправочной магистрали и закрывается при достижении указанной степени заполнения баллона. Ограничение максимального наполнения баллона необходимо для предотвращения чрезмерного повышения давления в нём в случае нагрева (например, на солнце в жаркую погоду)
Мультиклапан также может содержать в себе предохранительный клапан (стравливает газ при высоком давлении, например при перегреве баллона), пробку из легкоплавкого сплава (не допустить взрыва баллона при пожаре, сбросить газ в атмосферу, чтобы он просто сгорел) и дополнительный вентиль для отбора в двигатель паровой фазы при запуске холодного двигателя. Однако, наличие данных компонентов в мультиклапане не обязательно.
Баллоны для сжатого природного газа находятся на раме, под полом салона автобуса или на его крыше. Сжатый метан находится под давлением до 200 атмосфер. Несколько баллонов объединены в общую магистраль, имеется общий заправочный вентиль, каждый баллон также имеет собственный вентиль.
Газ из общей магистрали поступает в испаритель (подогреватель) — теплообменник, включён в систему жидкостного охлаждения, после прогрева двигателя газ подогревается (сжиженный газ испаряется) до температуры ≈75 °C. Далее газ проходит через магистральный фильтр.
Затем газ поступает в двухступенчатый газовый редуктор, где его давление снижается до рабочего. Современные газовые редукторы обычно совмещают эти два устройства (испаритель и собственно редуктор) в едином устройстве[2].
Далее, газ поступает в смеситель (или в карбюратор-смеситель или в смесительную проставку под штатным карбюратором, определяется конструкцией топливной аппаратуры). В силу того, что в смесителе происходит смешивание двух газов, их конструкция существенно проще чем конструкция бензиновых карбюраторов[3], в которых происходит смешивание двух разных фаз — жидкой (бензин) и газообразной (воздух), из-за чего в конструкции карбюратора имеются довольно сложные системы для поддержания постоянного состава смеси при разных расходах.
Двигатели разделяются на:
- специальные (или модифицированные), предназначенные только для работы на газе, бензин используется краткосрочно при неисправности газовой аппаратуры, когда нет возможности произвести ремонт на месте;
- универсальные, рассчитанные на длительную работу как на газе, так и на бензине.
Бензобак и топливный насос на автомобилях с газовыми двигателями сохраняются.
В холодное время года запуск двигателя, работающего на сжиженном газе производится путём отбора паровой фазы, после прогрева испарителя происходит переключение на жидкую фазу. Однако, для бензиновых двигателей, переоборудованных для работе на газе, крайне рекомендуется[4] пуск двигателя осуществлять на бензине, а на газ двигатель переключать после прогрева до температуры 40-50 °C.